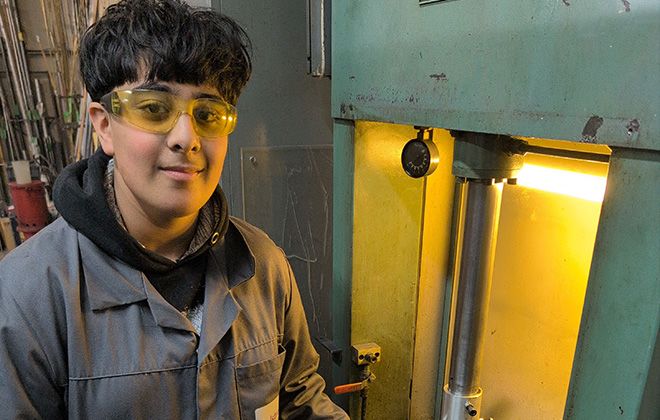
The future of a business is only guaranteed with a long-term strategy designed to ensure sustainable growth. New ideas and moving with the times are essential and one way of ensuring this happens is through the recruitment of apprentices.
James Valentine, Director at engineering business Solstrand Industries, explains: “In our early action planning, we identified a need for bringing in new talent, with the attitude we need, so they could be trained. Our mantra has always been ‘hire for attitude, train for skill.’
"The strategic reason for going down the apprenticeship route was risk management and succession planning. Many companies would be hesitant to take the apprenticeship route because everyone knows a couple of interviews are not enough to guarantee a match and identify somebody who will be good for you in a year. That is understandable, but we decided it was a risk we had to take.”
Being open to new ideas
James took over the business in April 2023 with business partner Vernon Bacchus. Solstrand, based in High Wycombe, is a subcontract engineering company specialising in the production of certified precision components and assemblies for the aerospace industry, mostly centred on radio frequency equipment such as antenna mounts. There are 11 employees and one apprentice engineer, Abu-Bakr Siddique, who joins a rich history of apprentices at the company.
“One of our employees started as an apprentice here in 1982 and he's still here,” says James. “There's a very clear need to retain people and train them our way. We're very open to taking on new ideas and when we are working with a training partner, we know the apprentice is receiving the most up-to-date input on health and safety and project management.”
External support guides Solstrand through the recruitment process
James recently attended a Buckinghamshire Business First Engineering Sector Employer Group meeting where he explained more about the help Solstrand received: “Like many employers, I initially approached the apprenticeship route with caution, wary of the potential bureaucracy and complexity involved. However, (training partner) Oxfordshire Advanced Skills (OAS) provided invaluable support, guiding me through the process and simplifying the path to bringing an apprentice on board.
“The OAS team have helped with the process in many ways, including with recruitment and the initial vetting. I wrote the job description, but they promoted that to their talent pool who are already approved to be at the right level for the apprenticeship they offer. The recruitment service covered everything down to shortlisting candidates and even scheduling them for interviews on days I'd said I was available.”
Through that process they found 16-year-old Abu who now runs the machinery and is learning to programme it while also developing finishing skills, with work having to be completed by hand. “There is an artisanal element to our work," says James. "Unlike an automotive parts manufacturer producing a small range of parts at massive volume, it can be more challenging to make a broad range of parts in small batches to very tight tolerances. That needs to be learned on the job and is measured in years, not months.”
How the apprenticeship works
Abu is on a Machining Technician Pathway programme, working on site for four weeks before spending four weeks with training partner Oxfordshire Advanced Skills, whose training facility is based in Culham, Oxfordshire. The facility is run by training group MTC which specialises in the engineering sector.
“There's a very high standard of training there," says James. "In the factory he is trained by our lead Computer Numerical Control programmer who effectively manages his engineering training, and our Managing Director Vernon looks after the administration. I deal with his academic contacts, his assessor, and his progress reviews."
Creating positive futures
James’ commitment is further illustrated by the contract given to apprentice engineers at Solstrand. “It is virtually identical to the contract we would give a trainee engineer at a higher pay grade who isn't going through an apprenticeship," explains James. "If they work effectively and engage with the apprenticeship programme, we will keep them on. Our arrangement with these apprentices is fully intended to be long-term.”
Solstrand aims to recruit a new apprentice every year, ensuring it continues to evolve effectively and sustainably with the future very much in mind. The company is also a signatory of the Tomorrow’s Engineers Code which is committed to increasing the number and diversity of young people entering engineering and technology careers.
“It's not a short-term thing," confirms James. "We are a business dedicated to the process of modernisation around skills, machinery and process. We invest in our people and we really mean that.”
Want to learn more about hiring an apprentice?
John Browning, Workforce Skills Programme Manager at Buckinghamshire Business First, adds: “It’s important businesses understand that with the right support and direction it can be easy to take on an apprentice.
“It is not a daunting process and can provide a solution to skills shortages. The team at Buckinghamshire Business First are here to help on that journey.”
Contact our Workforce Skills Team for more information. Call 01494 927130, email [email protected], or book a chat via this online form.
Photo: Apprentice engineer Abu-Bakr Siddique operating a hydraulic press to manufacture an anchor plate used for holding a conductor to the wing of an aircraft.