- By Mathew Moslehi, IMSM Ltd, Buckinghamshire Business First Ambassador
- 28 November, 2016
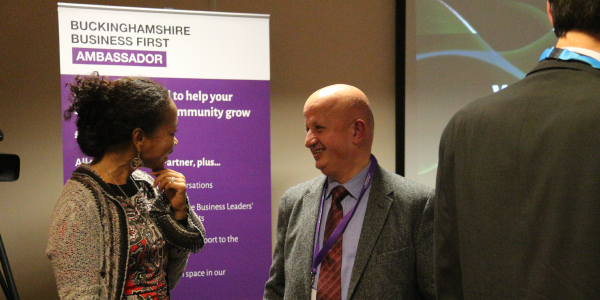
Share by email
The Yorkshire saying ‘where there's muck there’s brass' covers the waste of physical resources, but waste comes in many forms, including energy, staff time and much else, all of which reduce business profits. Up to 30 per cent of operating costs arise from non-value added processes and procedures which often represent low hanging fruit.
What is waste?
Waste can be defined as “any process or procedure which doesn’t add value to your product or service”. For example, you may recognise a number of these wastes:
- Overproduction (of your products or services)
- Waiting (whether waiting for a decision, repair, quality check, review, delivery or a payment from a customer, resources are used up)
- Transport (this can be the internal and external movement of goods, equipment, information and people within your system)
- Inappropriate processing (Are you using the right tools, process or person for the job? Does that person have the right skills, training and experience?)
- Unnecessary inventory (this can be raw materials, finished goods, works-in-progress, or debtors)
- Unnecessary motion (your working environment should be in right order)
- Returned goods / defects arising from errors (these can arise because of poor planning, workmanship or missed deadlines)
- Talent (underutilising people's talents, leaving you short of skills and knowledge)
Waste reduction
Reducing waste requires a systematic and methodical approach to streamlining processes and improving business efficiency – a Quality Management System – and the key to such a system is the use of Quality (ISO) standards.
The use of a Quality Management System based on ISO standards enables businesses to:
- Increase customer satisfaction through improved safety, quality and processes
- Increase profits by driving down costs, boosting productivity and improving the bottom line
Quality business
Satisfying existing customers and improving returns is only the beginning: the greater gains come from opening the way to new business. Increasingly, contracts and supply chains are only open to standards-compliant businesses and give an advantage to bigger competitors. Implementing standards enables you to compete with larger organisations on a level playing field and to inspire confidence in your business, to set you apart from the competition and open doors to new markets.
Certification with an international standard gives you international reach and ensures your managements systems run as smoothly and cost-effectively as possible. Benefits of ISO 9001 certification include:
- International recognition – open up your organisation to clients both home and abroad
- Streamlined internal processes – improving efficiency, accountability and traceability whilst maintaining expenses and savings
- Improved staff motivation – team are motivated to succeed due to time and resources being spent on what matters
- Inspires trust - a strong customer focus improves your customer service and referrals
- Improved processes and customer services – increases your competitive edge and sales growth potential
- Quality at the forefront – regular reviews ensures quality is consistently at the forefront of the business
Getting started
UK government figures indicate that of all the investments businesses make, the implementation of quality standards has perhaps the greatest effect in terms of the multiplier effect.
Any business would be well advised to seek out an accredited quality consultant and get started: the sooner you begin, the sooner your business will improve.